Basic Info.
Model NO.
H13 tool steel
Special Use
High-strength Steel Plate, Wear Resistant Steel, Silicon Steel, Cold Heading Steel, Free Cutting Steel, Mold Steel
Application
Tool Steel Bar
Transport Package
Wooden
Specification
6-400mm
Trademark
Smooth
Origin
China
HS Code
7214100000
Production Capacity
5000
Product Description
1.2344/SKD61/H13 Tool Steel/
H13 Tool Steel is a 5% Cr hot work tool steel with good combination of properties such as high toughness and hot resistance. Its alloy design makes H13 a very versatile tool steel, employed in several application in hot work tooling and also in plastic moulds. In service, H13 presents the following behaviour:
- Good homogeneity of properties in all directions;
- High resistance to heat-checking and gross cracking;
- Good machinability and polishability;
- High hardenability and good dimensional stability during heat treating.
- Good heat conductivity.
Because of its high toughness and very good stability in heat treatment, H13 is also used in a variety of cold work tooling applications. In these applications, H13 provides better hardenability (through hardening in large section thicknesses) and better wear resistance than common alloy steels such as 4140.
Also available as Electro-Slag-Remelted (ESR) products as well. The remelting processes provide improved chemical homogeneity, refinement of carbide size, and the associated improvements in mechanical properties and fatigue properties.
1.Size Range for H13 Tool Steel
H13 Steel Round Bar: diameter 80mm~420mm
H13 Steel Plate: thickness 25mm~400mm x width 200mm~800mm
Delivery Condition:
Tured Round Bar,Milling Plate,Black,requiremts for customers.
Spheroidizing Annealing,ESR material.
2.H13 Tool Steel Equivalent Grades
3.H13 Tool Steel Chemical Composition
4.H13 Tool Steel Mechanical Properties
Approximate tensile strength at room temperature.
The mechanical properties of H13 tool steel at annealed condition are not good enough to withstand the high stress and high friction environment because its hardness level is about 15RC, which is significantly lower than the practically required hardness of 49RC. So in order for H13 tool steel to be applicable for such hot working environment, the material must undergo a series of hardening process to increase the material hardness, and also surface hardening, such as nitriding to improve the wear resistance.
5.Forging of H13 Tool Steel
6.Heat Treatment for H13 Tool Steel
Soft Annealing
Protect the steel and heat through to 1560°F (850°C). Then cool in the furnace at 20°F (10°C) per hour to 1200°F (650°C), then freely in air.
Stress Relieving
After rough machining the tool should be heated through to 1200°F (650°C), holding time 2 hours. Cool slowly to 930°F (500°C), then freely in air.
Hardening
Pre-heating temperature: 1110-1560°F (600-850°C), normally in two pre-heating steps.
Austenitizing temperature: 1870-1920°F (1020-1050°C), normally 1870-1885°F (1020-1030°C).
Quenching
Quench in still air or dry air blast. If complicated forms are to be hardened, an interrupted oil quench can be used. Quench part in oil and remove from bath when it just loses its color (1000°-1100°F). Finish cooling to below 150°-125°F in air, then temper immediately.
Tempering
For hot work applications, H13 is used in the hardness range of HRC 38 to 48. The usual hardness range for die casting dies is HRC 44 to 48 requiring a temper at approximately 1100°F. For improved shock resistance, the steel is often tempered at temperatures approaching 1150°F, resulting in hardnesses of HRC 40 to 44. The steel should be held at the tempering temperature for at least two hours per inch of greatest cross section. All hot work steel should be tempered at a minimum of 50 degrees above the expected maximum operating temperature of the tool or die. Double tempering, with the second temper of 25 to 50 degrees lower than the first temper is always advisable, particularly where heat checking is a problem.
7.Applications of H13 Tool Steel
Tools for Extrusion
Plastic Molding Application
Other Applications
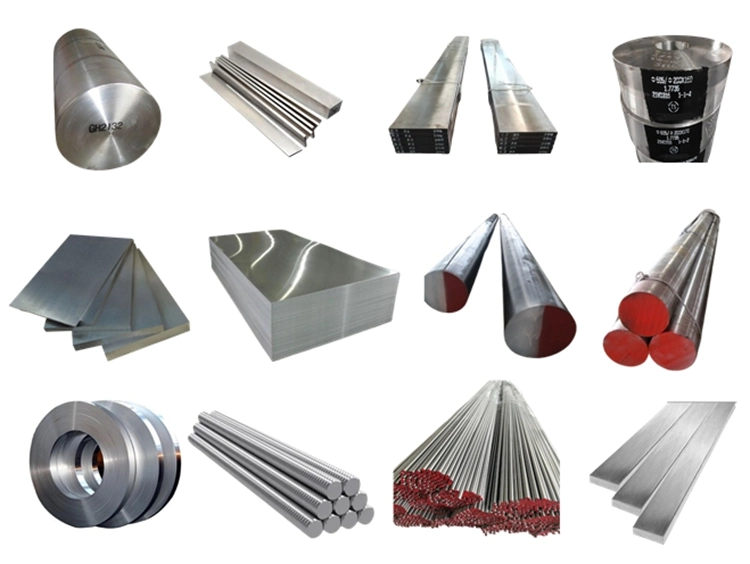
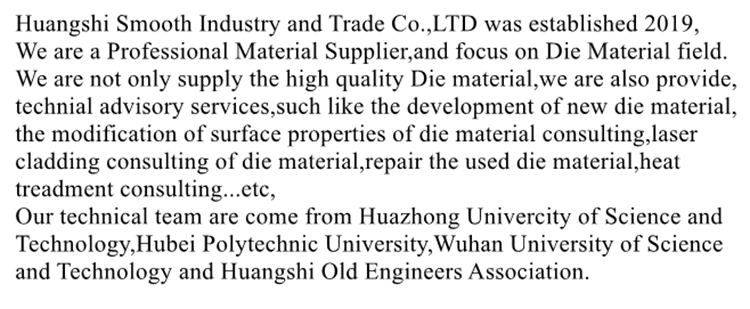

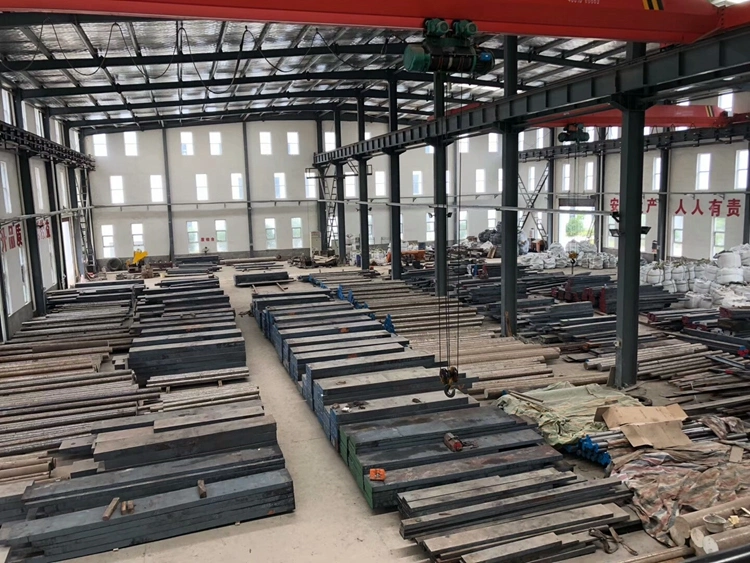
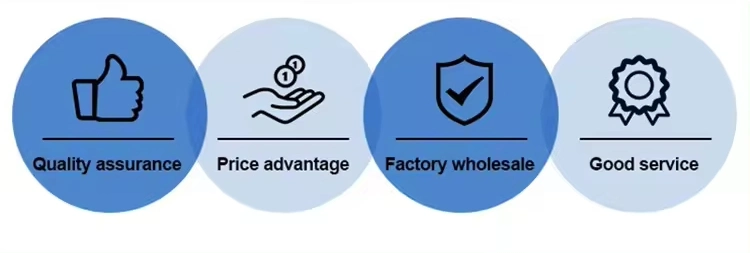
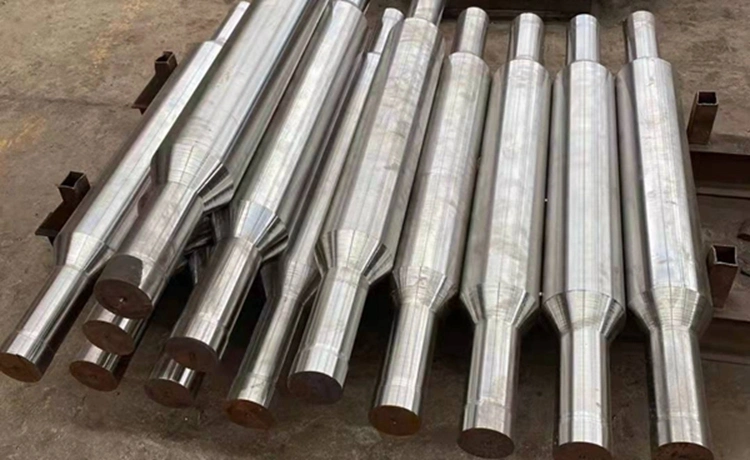

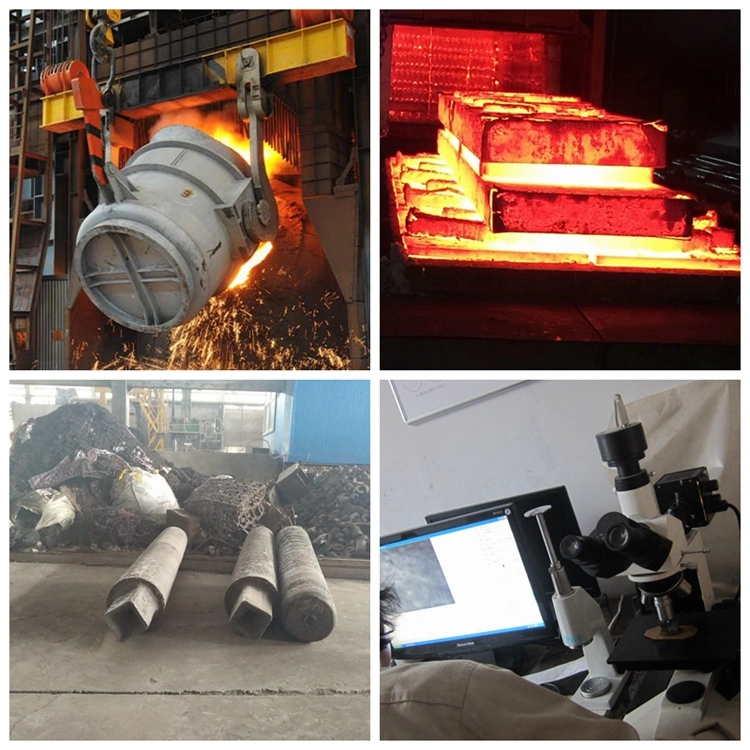
The above is just a brief introduction of H13 Tool Steel,which is unlikely to be explained in detail here.If you have any questions about it ,please feel free to leave us a message,so we could discuss it together!
H13 Tool Steel is a 5% Cr hot work tool steel with good combination of properties such as high toughness and hot resistance. Its alloy design makes H13 a very versatile tool steel, employed in several application in hot work tooling and also in plastic moulds. In service, H13 presents the following behaviour:
- Good homogeneity of properties in all directions;
- High resistance to heat-checking and gross cracking;
- Good machinability and polishability;
- High hardenability and good dimensional stability during heat treating.
- Good heat conductivity.
Because of its high toughness and very good stability in heat treatment, H13 is also used in a variety of cold work tooling applications. In these applications, H13 provides better hardenability (through hardening in large section thicknesses) and better wear resistance than common alloy steels such as 4140.
Also available as Electro-Slag-Remelted (ESR) products as well. The remelting processes provide improved chemical homogeneity, refinement of carbide size, and the associated improvements in mechanical properties and fatigue properties.
1.Size Range for H13 Tool Steel
H13 Steel Round Bar: diameter 80mm~420mm
H13 Steel Plate: thickness 25mm~400mm x width 200mm~800mm
Delivery Condition:
Tured Round Bar,Milling Plate,Black,requiremts for customers.
Spheroidizing Annealing,ESR material.
2.H13 Tool Steel Equivalent Grades
Country | USA | German | Japan | China | |
Standard | ASTM A681 | W-nr. | DIN | JISG4404 | GB/T1299-2000 |
Grades | H13 | 1.2344 | X40CrMoV5 | SKD61 | 4Cr5MoSiV1 |
3.H13 Tool Steel Chemical Composition
Grades | C% | Si% | Mn% | P% | S% | Cr% | Mo% | V% |
H13 | 0.32~0.45 | 0.80~1.20 | 0.20~0.50 | ≤0.03 | ≤0.03 | 4.75~5.50 | 1.10~1.75 | 0.80~1.20 |
1.2344/X40CrMoV5 | 0.37~0.42 | 0.90~1.20 | 0.30~0.50 | ≤0.03 | ≤0.03 | 4.80~5.50 | 1.20~1.50 | 0.90~1.10 |
SKD61 | 0.35~0.42 | 0.80~1.20 | 0.25~0.50 | ≤0.03 | ≤0.02 | 4.80~5.50 | 1.00~1.50 | 0.80~1.15 |
Approximate tensile strength at room temperature.
Properties | 52HRC | 45RHC |
Tensile strength | 263,000psi 1820N/mm2 | 206,000psi 1420N/mm2 |
Yield strength | 220,000psi 1520N/mm2 | 185,000psi 1280N/mm2 |
Reduction of area | 50% | 50% |
Poisson ratio | 0.27~0.30 | 0.27~0.30 |
5.Forging of H13 Tool Steel
Items | Heating temperature | Starting forging temperature | Final forging temperature | Cooling |
Ingot | 2084~2156°F (1140~1180°C) | 2012~2102°F (1100~1150°C) | 1562~1652°F (850~900°C) | Slow cooling(in hole or sand) |
billet | 2048~2102°F (1120~1150°C) | 1922~2012°F (1050~1100°C) | 1562~1652°F (850~900°C) | Slow cooling(in hole or sand) |
6.Heat Treatment for H13 Tool Steel
Soft Annealing
Protect the steel and heat through to 1560°F (850°C). Then cool in the furnace at 20°F (10°C) per hour to 1200°F (650°C), then freely in air.
Stress Relieving
After rough machining the tool should be heated through to 1200°F (650°C), holding time 2 hours. Cool slowly to 930°F (500°C), then freely in air.
Hardening
Pre-heating temperature: 1110-1560°F (600-850°C), normally in two pre-heating steps.
Austenitizing temperature: 1870-1920°F (1020-1050°C), normally 1870-1885°F (1020-1030°C).
Temperature | Soaking Time (Minutes) | Hardness before tempering | |
°F | °C | ||
1875 | 1025 | 30 | 53±2 HRC |
1920 | 1050 | 15 | 53±2 HRC |
Quench in still air or dry air blast. If complicated forms are to be hardened, an interrupted oil quench can be used. Quench part in oil and remove from bath when it just loses its color (1000°-1100°F). Finish cooling to below 150°-125°F in air, then temper immediately.
Tempering
For hot work applications, H13 is used in the hardness range of HRC 38 to 48. The usual hardness range for die casting dies is HRC 44 to 48 requiring a temper at approximately 1100°F. For improved shock resistance, the steel is often tempered at temperatures approaching 1150°F, resulting in hardnesses of HRC 40 to 44. The steel should be held at the tempering temperature for at least two hours per inch of greatest cross section. All hot work steel should be tempered at a minimum of 50 degrees above the expected maximum operating temperature of the tool or die. Double tempering, with the second temper of 25 to 50 degrees lower than the first temper is always advisable, particularly where heat checking is a problem.
7.Applications of H13 Tool Steel
Tools for Extrusion
Part | Aluminium,magnesium alloys,HRC | Copper alloys HRC | Stainless steel HRC |
Dies,Backers,die-holders,liners,dummy blocks,stems | 44~50 41~50 | 43~47 40~48 | 45~50 40~48 |
Austenitizing temperature | 1875~1885°F (1020~1030°C) | 1900~1920°F (1040~1050°C) |
Part | Austenitizing temperature | HRC |
Injection molds compression, Transfer molds | 1870~1885°F(1020~1030°C) Tempering 480°F(250°C) | 50~52 |
Application | Austenitizing temperature | HRC |
Severe cold punching,scrap shears | 1870~1885°F(1020~1030°C) Tempering 480°F(250°C) | 50~52 |
Hot shearing | 1870~1885°F(1020~1030°C) Tempering 480°F(250°C) or 1070~1110°F(575~600°C) | 50~52 45~50 |
Shrink rings(e.g. for cemented carbide dies) | 1870~1885°F(1020~1030°C) Tempering 1070~1110°F(575~600°C) | 45~50 |
Wear resisting parts | 1870~1885°F(1020~1030°C) Tempering 1070°F(575°C) nitrided | Core 50~52 surface~1000HV1 |
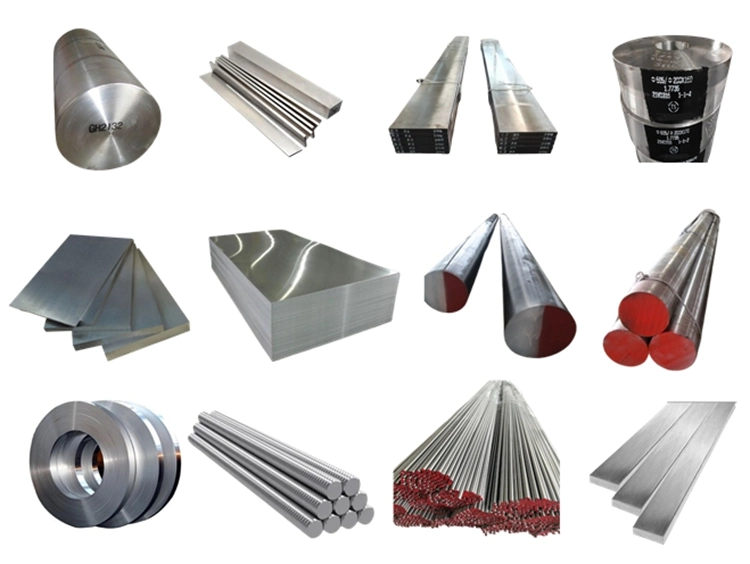
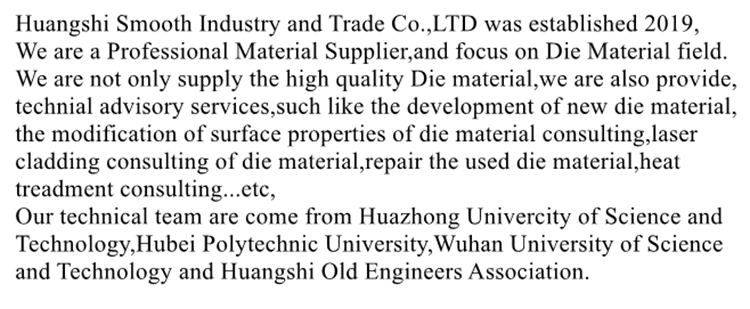

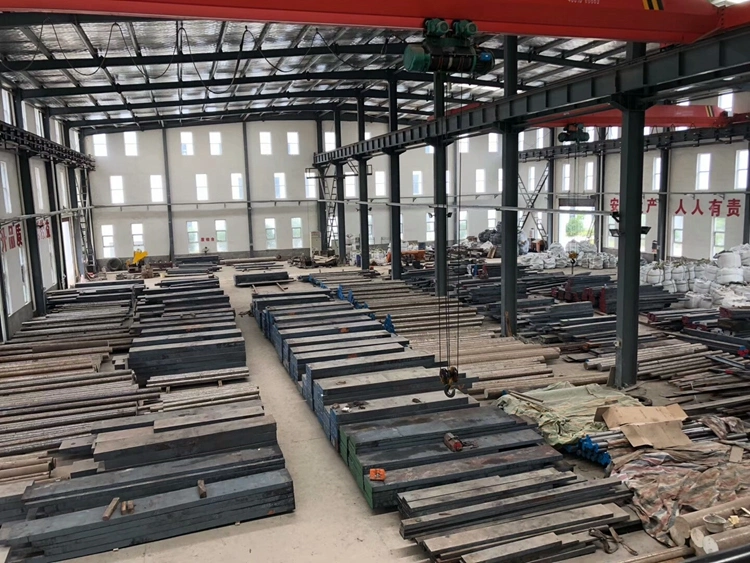
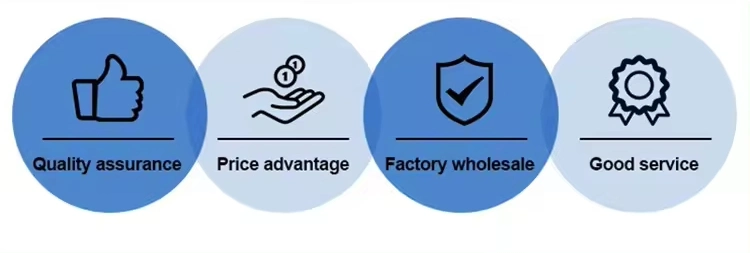
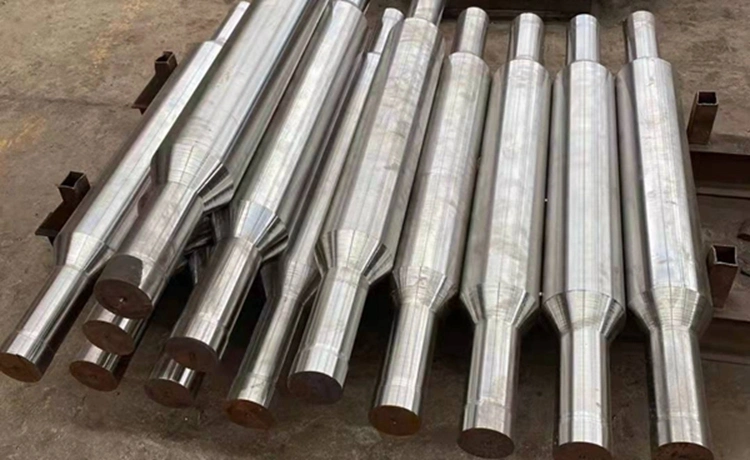

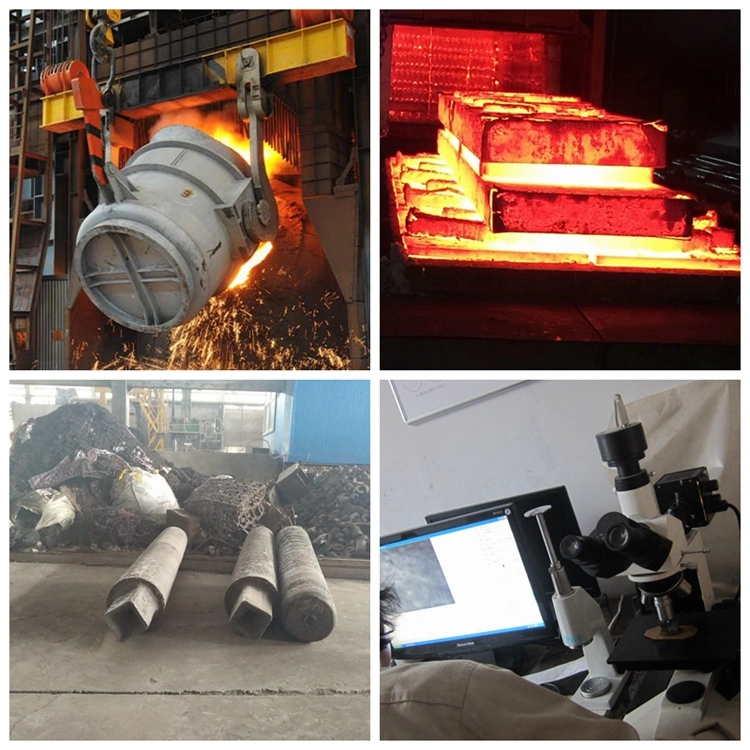

The above is just a brief introduction of H13 Tool Steel,which is unlikely to be explained in detail here.If you have any questions about it ,please feel free to leave us a message,so we could discuss it together!